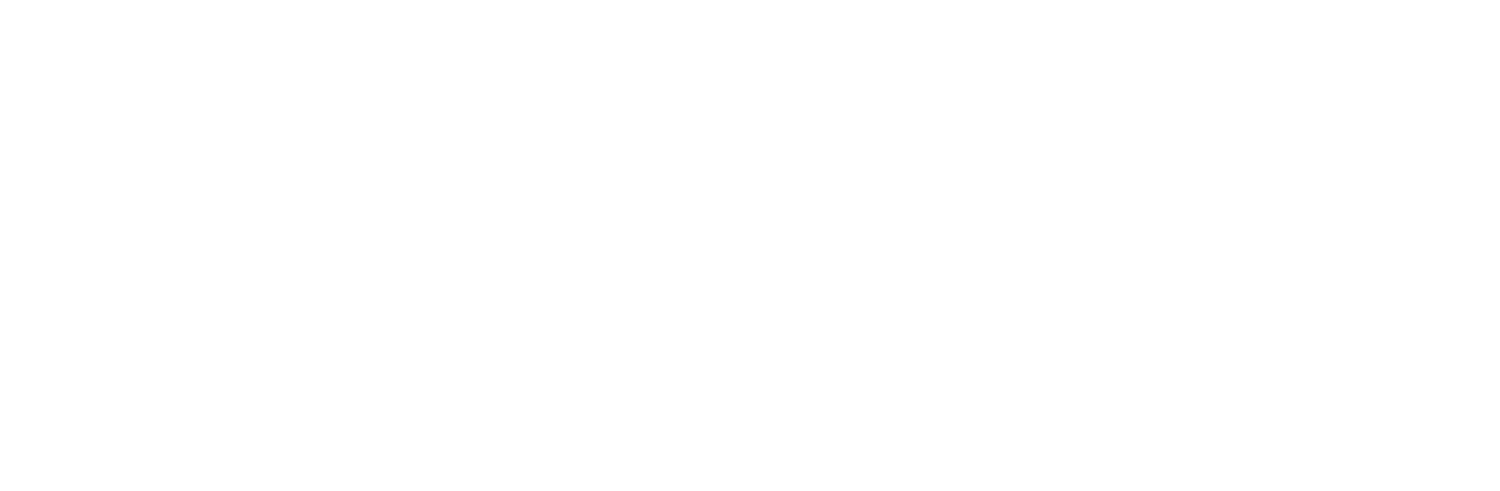
Industry 4.0
What it is and why it matters
Industry 4.0 – the fourth industrial revolution – brings together digital and physical worlds using sensors, the Industrial Internet of Things (IIoT) and technologies such as artificial intelligence and machine learning. These technologies are embedded across R&D, manufacturing, supply chain, logistics and other business areas to capture and analyze real-time data to transform how parts and products are made, warehoused, used and maintained.
History of Industry 4.0
Industry 4.0 is ushering in a new digital reality – one that is fundamentally altering the rules of production, operations and work. With the first industrial revolution, water and steam power mechanized manual work. In the second, electricity and assembly lines enabled cost-efficiency. In the third, we harnessed computers and mass automation to do things faster, better and smarter. The fourth industrial revolution builds on previous work by making factory systems – and the processes they support – smart, autonomous, real time, and connected across supply chains and entire ecosystems.
The origins of Industry 4.0 began in 2010 when the German Federal Ministry of Education and Research began exploring emerging high-tech trends and their potential to benefit society and enable people – and companies – to do more with less. The first official use of the term Industry 4.0 emerged the next year when companies around the globe began to talk seriously about its potential.
Things took off quickly at this point, as people realized the internet could be used to simplify data collection, relay digital data and enable the Internet of Things (IoT), which was already gaining traction in other countries. Over time, countries have collaborated to improve interoperability, enable digital data collection and real-time data analysis with full virtualization, and harness the IoT.
Today, Industry 4.0 is a reality – not just a concept – that can be fully realized as part of large and small digital transformation initiatives and smart factories. Across industries, companies are engaged in digital transformation of their production processes, assembly lines and asset-intensive operations using Industry 4.0 technologies.

Volvo Trucks
Learn how these subsidiaries of Swedish manufacturer AB Volvo minimize unplanned downtime using remote diagnostic and preventative maintenance services based on IoT technologies, analytics and AI from SAS.
IoT data with artificial intelligence reduces downtime, helps truckers keep on trucking.
Industry 4.0 in today’s world
By moving to real-time data access and continuous intelligence enabled by Industry 4.0 technologies, businesses are fundamentally transforming how they run operations and conduct business.
Who’s using Industry 4.0?
Industry 4.0 will increasingly power the production processes for every successful organization – and those that invest today in smart machines and smart factories will soon be market leaders. Explore how industries across the world are using Industry 4.0 to achieve their digital transformation and strategic business goals.
IoT data only brings value if you start analyzing the data and making smarter decisions.

Georgia-Pacific is an Industry 4.0 success
Georgia-Pacific relies on sensor data, IoT and machine learning to improve efficiency, reduce downtime and respond to market conditions.
How Industry 4.0 works
Integration that enables real-time data flows between digital systems is nothing new. But capturing real-time data from the physical world and using it to enable large-scale, machine-to-machine communication (M2M) to intelligently drive autonomous production processes in factories, supply chains, warehouses and beyond is new – and central to Industry 4.0. Even greater value is possible when data from production operations is merged with operational data from R&D, CRM, ERP, supply chain, warehousing and logistics, and customer service systems. Companies can achieve new levels of efficiency, automation, uptime and customer responsiveness – and enable entirely new business and service models.
Delivering on such value propositions is enabled by a wide range of new technologies such as:
- The Internet of Things (IoT). IoT-connected devices and machines can improve how we work and live, and how assembly lines and other production processes, logistics systems, supply chains and other business operations work. For example, IoT can enable a smart factory that monitors industrial machines to look for problems and then automatically adjusts operations to avoid failures.
- Big data. Big data describes large, hard-to-manage volumes of data – both structured and unstructured – that inundate businesses daily. But it’s not the amount of data that’s important. It’s what organizations do with the data that matters. Big data can be analyzed for insights that lead to better decisions and strategic business moves.
- Cloud computing. Cloud computing is a subscription-based delivery model that provides scalability and fast, cost-efficient delivery of data – even in real time – across organizational systems. It also supports IoT capabilities, which can in turn enable more efficient operations and new business models.
- Artificial intelligence (AI) and machine learning. AI makes it possible for machines to learn from experience, adjust to new inputs and perform humanlike tasks. Machine learning, a branch of AI, is a method of data analysis that automates analytical model building and enables systems to learn from data, identify patterns and make decisions with minimal human intervention – capabilities that are essential for enabling autonomous smart factories.
- Digital twins and simulations. Industry 4.0 enables organizations to collect data and use it to create a virtual, digital twin (replica) of business elements or areas such as a production line, smart factory and supply chain. This digital twin can be used to simulate operational changes, process modifications and other variables to understand their impact, make adjustments and inform decisions before changes are implemented.
- 3D printing and additive manufacturing. With 3D printing, manufacturers can centralize product and part design – stored as digital code – and use 3D printing to create prototypes, and then allocate production at flexible smart factories with available capacity or in smaller smart factories close to the customer. This enables shorter production runs for reduced materials and logistics costs and greater market responsiveness. Looking ahead, rather than centrally manufacturing shipping and warehousing a part, customers will be able to purchase and download blueprints for parts and 3D print or machine them locally.
- Edge computing. Edge computing enables data to be analyzed at or near where it is created (for example, on a piece of equipment on an ocean-based oil rig) and action to be taken based on the analytical results. There’s no need to move data to a server environment for analysis, which takes time and may not always be possible. By eliminating data transfer time, edge computing reduces data latency and response times.
- Cyber-physical systems (CPS). Cyber-physical systems are smart machines that bring together computer-assisted software components and internet-connected mechanical and electronic parts that communicate with data centers, enabling semi-autonomous or autonomous decisions and operations. In production processes, they assist smart manufacturing by improving a factory’s flexibility, productivity and ability to adapt to meet new market demands.
- Autonomous mobile robots (AMRs). Autonomous robots have long been used to perform complex tasks with great speed and accuracy – for example, on assembly lines – and they will increasingly work alongside humans and learn from them using machine learning. AMRs intelligently navigate facilities, avoiding obstacles to collecting and sharing big data (such as environmental conditions) from within a fleet or facility. This real-time data and visibility can be used to automate corrective actions or enable people to make informed, timely decisions that improve business outcomes.
- Horizontal and vertical system integration. Horizontal integration refers to networking between individual machines, pieces of equipment and/or production units. Vertical integration typically refers to connecting and controlling different parts of the business and extended supply chain, including partners and suppliers. With Industry 4.0, a company's departmental functions and capabilities will be integrated to operate in greater unison across the enterprise and enable truly automated value chains.
- Cybersecurity. Cybersecurity refers to technologies, processes and controls that work together to protect systems, networks and data from cyberattacks. This is critical to companies investing in Industry 4.0-enabled digital transformation.
Industry 4.0 technologies at work: The smart factory
To better understand how these technologies deliver on the promise of Industry 4.0, let’s explore how they enable smart factories. In a smart factory, advanced analytics (such as machine learning) can process the big data being created via smart sensors and the IoT, including more agile processes to integrate the data and keep pace with customer demand. They can make products on demand, source numerous suppliers from around the world and manage customer feedback via social media before their customer service representatives ever hear the complaint. Smart factories allow companies to stream data in real time, gleaning insights that allow on-the-spot changes in source materials, machine functionality and even customer service. In this way, IoT-enabled smart factories can:
- Produce a higher quality product.
- Improve internal production processes.
- Enhance customer experiences (CX).
A better product
Smart factories allow companies to stream real-time data, gleaning insights that allow on-the-spot changes in source materials, machine functionality and even customer service. Smart sensors, for instance, can ensure that every item – be it an article of clothing or cutting-edge medical equipment – has the same quality level as the one before. Imagine how many millions of dollars this could save in lost products, customer complaints and damage to a company’s brand. In fact, IoT in manufacturing helps ensure that once a defect is found, the smart machine can be taught to self-correct and potentially prevent that defect before additional errors occur. The result is better products and fewer losses.
A smarter process
Industry 4.0 technologies reduce the risk of a major loss resulting from unscheduled maintenance, which halts production and hurts employee productivity. In smart factories that employ the Industrial IoT, sensors enable manufacturers to automatically monitor wear and tear in real time. Machine learning can create precise models unique to each process that can track time to replacement for parts and machinery. For example, if the cutting blades in a paper factory dull slightly, it may create a ragged edge that consumers dislike – one that could take several reams for a human inspector to catch. Predictive maintenance can help schedule blade replacement before that error ever occurs. Even better, it can schedule the replacement for offline hours so that no production time is ever lost. This increases the overall agility of the company, which is what digital transformation is all about.
Happier customers
Faster, more agile production processes are just one part of the equation. By analyzing the big data that smart sensors capture while products are being used in customers’ workplaces, manufacturers can get a better sense of when, or if, products fail, how they’re being used and how to adjust the production process accordingly. Using advanced analytics such as text mining and machine learning, they can also quickly process public-facing comments made on social media about their products so they can attend to customer complaints in near-real time.
Industry 4.0 solutions
The SAS® Quality Analytic Suite offers data management, easy analytics model building, early-warning alerts and root-cause analysis.