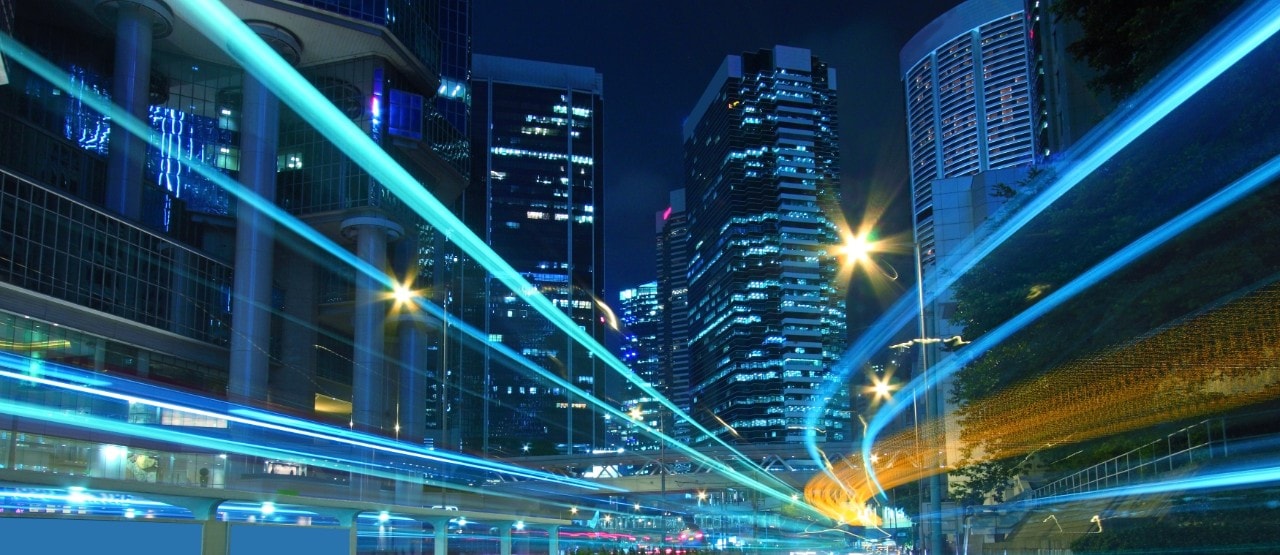
IoT challenges in the connected supply chain
By: Daniel Newman, Principal Analyst of Futurum Research and CEO of Broadsuite Media Group
If there’s one sector of today’s marketplace where the Internet of Things is poised to plan a shake-up, it’s the industrial sector. In fact, the impact in supply chain alone is expected to be so large – Cisco and DHL estimate more than $1.9 trillion1 – that the Industrial Internet of Things (IIoT) has even been given its own moniker. Still, that’s not to say the IIoT will lead to overnight success for today’s industrial manufacturers and other members of the connected supply chain. Far from it.
In a world where most companies are still using a mix of outdated legacy systems, new technology, and connected and unconnected assets, it will take a while for the IIoT to take full effect. Does that mean it’s not worth the investment? Of course not. But it does mean your company will face challenges as you prepare for the inevitable jump into the logistics world of the IIoT. The following are just a few.
Challenge No. 1: Internal struggle between operational management and IT teams
This is nothing new. With every great tech disruptor, companies must deal with a management issue. There will likely be some struggle between the operational management team and the IT team when it comes to purchasing IIoT devices for the connected supply chain. Many IT professionals might want to purchase the latest technology as soon as it hits the market, but operational management teams might not want to spend the money.
With the IIoT this is especially problematic, as operational teams are accustomed to purchasing technology that can last years if not decades. But IIoT devices most likely won't last years, validating your IT team's desire to purchase new technology. You will have to find a balance between purchasing new technology and using existing technology. The decision will most likely come down to whether or not a new IIoT device solves a problem or makes a bigger impact on employees and processes.
For example, the IIoT is set to eliminate barcode scanners by replacing UPC tracking with RFID technology and cloud-based GPS sensors that will be able to track the location of items immediately in a warehouse. It makes sense to upgrade to this technology right now because of the efficiency new RFID sensors will bring. But what happens in a year or so when new and potentially better GPS tracking software or RFID sensors are available?
Most companies will need to do a cost-benefit analysis with the help of both IT and operational management teams to determine if (and when) a new upgrade would make an impact that's worth the investment. Ultimately, I believe that waiting for what’s next at this point is a risky proposition. I recommend investing in flexible architectures that allow for a more agile approach to change, given how rapidly technology is changing and will continue to change in the future.
Challenge No. 2: Skills are complex – and lacking
Chances are good that you’re dealing with a highly varied employee pool – boomers finishing out their career in manufacturing and millennials just entering the workforce. All of them will have their own learning curve when it comes to preparing for the complex processes of the IIoT – and their own willingness to adopt it.
Yes, the IIoT is meant to simplify and make manufacturing and connected supply chains more efficient. But adopting the IIoT also means relinquishing quality control processes by trusting sensors and machines to determine when machines need scheduled maintenance, and using data to make decisions that used to be made by people right on the factory floor. It’s a complete change from the way business has been done in the past.
Offering training courses and compensation to continue education will prove to employees that they're just as necessary now as they were before the technology changes were implemented. Leadership can help change mindsets by reassuring employees that they are not obsolete in the connected supply chain.
This is an incredibly exciting time in digital revolution. Those in the industrial market are poised to reap many of the benefits of the IIoT if they have the patience and passion to weather the immediate challenges. Daniel Newman CEO, BMG & Principal Analyst Futurum Research
Challenge No. 3: Managing and analyzing all the data
One of the main assets of the IIoT, unquestionably, is the exponentially larger amount of data it makes available. And while this data can certainly contain valuable nuggets of information for the connected supply chain, simply collecting the data is not sufficient.
Raw data collected from sensors throughout the supply chain may be incomplete, insufficient or inaccurate. Not to mention that today’s supply chain doesn’t just include data from sensors and other connected systems and processes. It also tends to include data from offline processes and partners who are not yet running fully digital operations. And consider the data from traditional ERP systems versus the unstructured data that comes from social media sources.
All of this disparate data has to be properly accounted for and managed if a supply chain player expects to make fast, well-informed decisions, fix potential issues and capitalize on the data’s full value. Accomplishing this requires much more than basic data access. It requires using data integration, data quality, data governance and other essential data management functions to handle all the data that’s part of the supply chain. Only when this happens will connected supply chain players be able to rely on sophisticated analytics to uncover insights that inspire smarter decisions, plus the potential for a much-needed competitive edge.
Still, less than 2 percent2 of leaders feel they have a clear vision for how to implement the IIoT on a large scale across the supply chain. Connected supply chain leaders need to ask: Do we have an analytics process – and the right people and technology – in place for using all of that data? Do our teams know the right questions to ask – and the right trends to look for in all the new sources of real-time data?
Daniel Newman Talks IoT: Supply Chain
In this short video, Daniel Newman talks with Roger Thomas of SAS about the connected supply chain and how IoT technology provides new insights that enable supply chain players to track, measure and optimize business performance like never before.
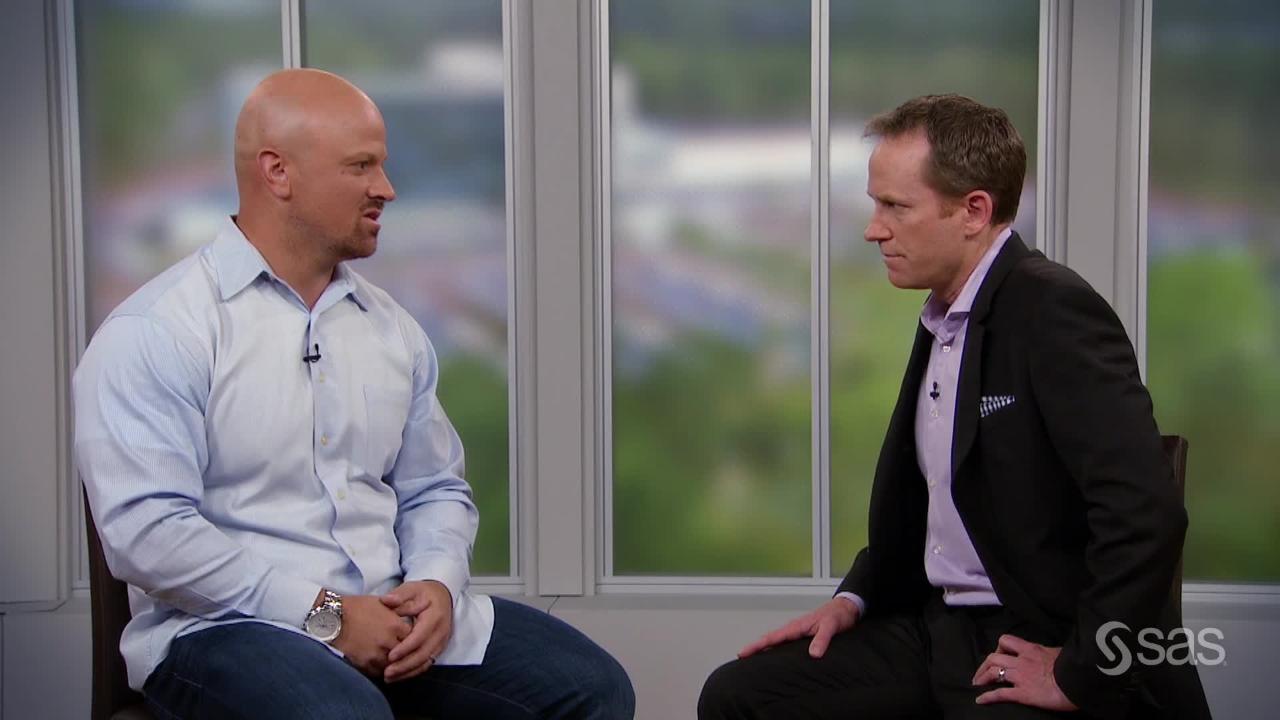
- 2x
- 1.75x
- 1.5x
- 1.25x
- 1x, sélectionné
- 0.75x
- 0.5x
- Chapitres
- descriptions désactivées, sélectionné
- Paramètres des sous-titres transcrits, ouvrir les paramètres des sous-titres transcrits
- Sous-titres transcrits désactivés, sélectionné
- English Sous-titres transcrits
This is a modal window.
Début de la fenêtre de dialogue. La touche d'échappement annulera et fermera la fenêtre.
Fin de la fenêtre de dialogue.
This is a modal window. Ce modal peut être fermé en appuyant sur la touche Échap ou activer le bouton de fermeture.
This is a modal window. Ce modal peut être fermé en appuyant sur la touche Échap ou activer le bouton de fermeture.
This is a modal window. Ce modal peut être fermé en appuyant sur la touche Échap ou activer le bouton de fermeture.
This is a modal window. Ce modal peut être fermé en appuyant sur la touche Échap ou activer le bouton de fermeture.

A balancing act for the connected supply chain
This is an incredibly exciting time in digital revolution. Those in the industrial market are poised to reap many of the benefits of the IIoT if they have the patience and passion to weather the immediate challenges. As I’ve noted before,3 there is so much to gain and very little to lose for those willing to jump in head first to ensure a competitive advantage.
Consider Maersk Line,4 which is one of the world's leading shipping companies. It added sensors to its refrigerated shipping containers that transmit vital information – like temperature and location – to a central hub. A team of employees can now manage issues as soon as they arise, regardless of the container’s location. As a result, containers require less manual inspection and are arriving to their destinations with consistently fresh produce.
Yes, more than 30 percent of executives believe there is a major skill gap in their companies when it comes to IoT readiness. Yes, security will remain a top concern in connecting so many different parts of your company’s infrastructure to the digital world. But from my viewpoint, the greater risk is lagging behind in what will surely be an unprecedented period in supply chain management. We’re talking no more barcodes. No more manual inspections. No more lost cargo, overripe produce, machine downtime or parts delays. We’re talking the most efficient manufacturing and connected supply chain this world has ever seen.
Join me and my co-host Brian Fanzo on SMACtalk as we speak with Roger Thomas of SAS about what leading companies are doing when it comes to supply chain optimization – including how they're structuring their IoT initiatives to create a competitive advantage for the business.
About the Author
Daniel Newman is the Principal Analyst of Futurum Research and the CEO of Broadsuite Media Group. He works with the world’s largest technology brands exploring digital transformation and how it influences the enterprise. He is regularly cited in CIO.Com, CIO Review, CNBC and hundreds of other sites across the world. A five-time best-selling author, including Building Dragons: Digital Transformation in the Experience Economy, Newman is also a Forbes, Entrepreneur and Huffington Post contributor, and a graduate adjunct professor.
References
1. How IoT Logistics Will Revolutionize Supply Chain Management.
2. IoT Readiness Remains a Challenge for Many Industrial Supply Chains.
3. IoT Driving Another Industrial Revolution.
4. Delivering the Goods: 8 Examples of IoT Transforming Supply Chain.
Recommended reading
-
ARTICLE Analytics leads to lifesaving cancer therapiesA long-shot treatment offers hope to 10-year-old Harrison after he learns the DNA profile of his cancer is resistant to chemo. Find out how data and analytics play a role in cancer research and cancer treatments that are saving lives.
-
ARTICLE 5 data management best practices to help you do data rightFollow these 5 data management best practices to make sure your business data gives you great results from analytics.
-
ARTICLE IT/OT convergence: The dilemma of the IoT perception gapTom Bradicich explains why IT/OT convergence is essential for successful IoT projects.
-
ARTICLE Game-changing technologies turn IIoT data into goldThe real value of IoT lies in its data. Maciej Kranz says technologies like edge and fog computing, machine learning and AI can unlock the hidden value in data from the IIoT.