Data visualization aiding to indemnify against freight damages and optimize cargo securing costs
Asian Paints uses SAS Visual Analytics to get up-to-the-day visibility of outbound logistics and fleet performance enabling operational decision making.
Committed to its strong consumer-focus and innovative spirit, Asian Paints turned to SAS Visual Analytics for its outbound logistics and analytical needs for transit damage reduction.
Asian Paints, India’s leading Paints Company, along with its subsidiaries have operations in 19 countries across the world with 26 paint manufacturing facilities, servicing consumers in over 65 countries. With such a complex supply chain coupled with high volumes of transactional data accumulating by the day, it was imminent to create a multi-level visibility across facilities to empower logistics managers for data-driven decision making.
With SAS Visual Analytics, the outbound logistics team no longer need to wait for end of the month to analyze the fleet performance and respective KPIs. Instead, executives have up-to-the-day visibility of latest insights based on refreshed data, which enables them to make nimble decisions swiftly and confidently.
From daunting to transformational
Before deploying SAS Visual Analytics, the corporate office used to download reports from different transactional systems for each of the many manufacturing plants in Excel every month. Transforming this information into a coherent dashboard was a daunting task because of the volumes of data. This monthly reporting sometime resulted in missed opportunities.
Where logistics analyses were previously done on a monthly level, with SAS Visual Analytics there’s a quick turnaround time of daily-level granular reporting enabling faster decision-making capabilities.
Ensuring data quality
Effective data manipulations were built in SAS Enterprise Guide, with necessary exceptional business logics and
scenarios designed in the process to harmonize data coming from varied transactional sources.
Utmost faith in the quality of the data enabled Asian Paints to make quick informed decisions and outpace the market.
SAS Visual Analytics helps Asian Paints reinforce that faith with confidence. With exhaustive data manipulations and business logics built in the solution, combined with an appealing interface, analysts can focus more on fetching answers rather than validating business scenarios.
Collaborative Visualizations
With SAS Visual Analytics, officers and logistics managers have the freedom to dissect their data and run their own analyses and discovery without requiring extensive IT support. They can generate and share their own reports, dashboards and visualizations simply by clicking or drilling into items of interest.
For example, senior management can take an extract of these reports before getting into vendor negotiations for revisiting contractual terms with existing and new fleet operators.
With compelling visualizations and easy drill-down capabilities, logistics executives can quickly decipher meaning of the data and make informed decisions. KPIs like ‘volume damage per ton’ are crucial and are monitored more closely with renewed focus. There seem to be a steady shift from reactive to proactive approach where more than damage incidents, the focus now is on the root-causes for the incidents and measures to quell them in future.
Having deployed SAS Visual Analytics, the logistics management team envisions to build on that foundation and gradually incorporate advanced sophistication through variants of cost apportionment analytics namely ‘Cost per ton’ and ‘Freight cost analyses’.
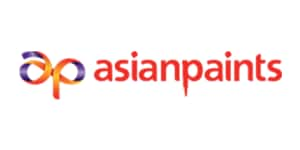
Challenge
- Reduce non-accidental damages by gaining visibility at a day level granularity.
- Dynamic reporting to optimize costs incurred in securing cargo.
Solution
Benefits
- Secure multi-level visibility with varying combinations to isolate transactions with maximum non-accidental damages.
- Identify root-causes for damages by route, truck, mode, product mix combination.
- Aiding to make informed decisions by securing in-transit cargo and for mitigating damage incidents.
- Identifying data patterns like seasonality and trends for deeper investigations to indemnify against damages.
- Quicker turnaround of reports and explorations at varying hierarchies.